Abstract
The purpose of this work is to study the influence of oil and surfactant present in produced water on the membrane distillation and membrane crystallization performance. The latter is evaluated in terms of permeate flux, quality of permeate and sodium chloride crystallization kinetics. Polypropylene and Hyflon AD40H/PVDF composite membranes with 0.2 \(\mathrm{\mu m}\) pore size were used in the investigation. The tests were carried out in direct contact configuration using two synthetic feed solutions: the first one without oil and surfactant, and the second one with oil and surfactant. The achieved results showed a permeate flux reduction of 20 and 40% for PP and AD40H, respectively, in membrane distillation and of 35% in membrane crystallization. These results may be attributed to the interaction between the salts and surfactant, which led to the deterioration of the membrane performance. Despite this, high salt rejection factors greater than 99.9% and total carbon rejections ranging between 80 and 90% indicated the good potential of membrane distillation technology for the treatment of produced water. Moreover, good quality crystals and high total water recovery factor (97%) were achieved using the membrane crystallization process. Nevertheless, the presence of oil and surfactant in the feed caused an increase in the induction time compared to the system without oil and surfactant. In addition, in the performed experiments, simple physical cleaning with distillate water was sufficient to recover the initial trans-membrane flux of the membranes.
Similar content being viewed by others
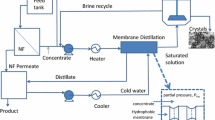
Avoid common mistakes on your manuscript.
Introduction
Fresh water is a basic need for human survival, as well as for all living organisms. For industrial, agricultural and domestic purposes, water is essential. Despite this, water scarcity is one of the greatest challenges of our time. The rapid population growth coupled with urbanization and industrialization activities has amplified the water demand and raised serious concerns about the sustainability and management of the natural resources currently available (Dinar et al. 2019; Huang et al. 2021). Although the efficiency of conventional methods of water use has improved, the growing water demand and the increasingly limited amount of clean water resources have led to the need to extract fresh water from non-conventional sources as well.
Produced water (PW) could be a potential source of potable water, especially for water-stressed oil-producing countries. PW is the largest by-product generated in oil and gas industries with a global estimated 3:1 volume-to-product ratio (Veil 2011). The composition of PW can vary considerably according to the geology and geographical location of the field, the type of hydrocarbon product, the life of the reservoir and the extraction method used (Wang et al. 2012; Coha et al. 2021). Nonetheless, most PW can be described as a mixture of complex organic and inorganic compounds including dissolved and dispersed oils, salts (such as sodium chloride and magnesium chloride), solid products, heavy metals, hydrocarbons, and various additives (Fakhru’l-Razi et al. 2009; Igunnu et al. 2014; Jiménez et al. 2018). The release of this water into the environment in the absence of adequate treatment becomes an important environmental problem (Gryta et al. 2001). Currently, the stringent environmental regulations adopted for PW discharge together with the rising costs of wastewater disposal are driving oil and gas industry to place greater emphasis on the treatment and reuse of PW (Igwe et al 2013). Physical, chemical, and biological methods have been introduced to treat PW prior to its discharge, resulting in the mitigation of its negative effects on the environment (Wang et al. 2012; Zheng et al. 2016; Ahmad et al. 2020; Coha et al. 2021; Goh et al. 2022). However, conventional treatment techniques have several drawbacks such as high costs, high energy consumption, use of hazardous chemicals, potential secondary pollution, low removal efficiencies of small oil droplets and emulsified oil (Hong et al. 2003; Chakrabarty et al. 2008; Abbasi et al. 2010; Nasiri et al. 2017).
The use of pressure-driven membrane processes (such as microfiltration (MF) (Silalahi et al. 2009; Motta et al. 2014; Karimnezhad et al. 2014), ultrafiltration (UF) (Wandera et al. 2011; Chang et al. 2019), nanofiltration (NF) (Tomer et al. 2009; Sadrzadeh et al. 2018), and reverse osmosis (RO) (Kim et al. 2011; Dastgheib et al. 2016) has provided a major breakthrough in treating PW due to their high oil removal efficiencies and easy operation. However, the performance of these processes is mainly hindered by membrane fouling problems (caused by oil droplets and/or soluble organic compounds), as well as by their high energy consumption. RO processes, for instance, suffer from significant limitations because of the high osmotic pressure of the feed stream at high solute concentrations (Wang et al. 2016); while the performance of the NF and MF membranes is limited by their inability to remove all dissolved components (Wang et al. 2015).
Over the past decades, membrane distillation (MD) technology has attracted significant interest in the treatment of oily wastewater. As it is well known, MD is a thermally driven membrane separation process in which only volatile molecules can be transported through a porous hydrophobic membrane (Boukhriss et al. 2023a, b). MD process could greatly benefit from the treatment of wastewater discharged at elevated temperatures because this could minimize the need to heat feed water before entering the membrane module (Dilaver et al. 2018). In addition, MD technology has been shown to be able to achieve high salt and organic carbon rejections even during hypersaline PW treatment (Alkhudhiri et al. 2012; Macedonio et al. 2014; Han et al. 2017; Ricceri et al. 2019; Gryta et al. 2020).
The ability of MD to treat high salinity feed water up to super-saturation has been well exploited in membrane crystallization (MCr) process, employed for simultaneously recovering fresh water and high-quality saline products from saturated solutions. (Ali et al. 2018) have used this process with the aim of recovering salts from microfiltered oilfield PW. The experimental results demonstrated that an integrated system can efficiently convert produced water into salt and freshwater, reducing waste disposal problems.
However, due to the highly hydrophobic nature of MD membranes, this process could present important practical limitations in the presence of the large and broad organic compounds, typical of PW (Estrada and Bhamidimarri 2016; Gonzalez et al. 2017). Depending on the nature of the organic contaminant, they may either induce the wetting phenomena or move freely across the hydrophobic membrane up to the final effluent (Chen et al. 2017; Franken et al. 1987; Kargbo et al. 2010; Wang et al. 2018). Additionally, MD presents other drawbacks which limit its commercial application such as low permeate flux compared to pressure-based membrane processes, membrane fouling and scaling, and trapped air within membrane pores that result in increased mass transfer resistance (Ameen et al. 2020).
Most of the studies to date have examined the influence of operating conditions, pre-treatment, and membrane surface modification on the MD process. However, few studies have examined the influences of oil and surfactants on MD and MCr processes.
(Gryta et al. 1999) investigated the application of MD for the concentration of O/W (oil-in-water) emulsions in direct contact configuration. The authors found that the permeate flux decreased significantly as the oil concentration in the emulsion increased, and that higher oil concentrations led to membrane pore-wetting and thereby reduced permeate quality. The authors deduced that the observed results were due to the reduced partial pressure caused by the presence of oil and to the affinity between hydrophobic oil and hydrophobic membrane.
The presence of surfactants in O/W emulsions was studied by Chen et al. (Chen et al. 2017). They reported stable MD performance of super-hydrophobic polyvinylidene fluoride (PVDF) membranes for feeds containing O/W emulsions when anionic surfactant was present. In contrast, in the presence of cationic surfactant, the MD performance in terms of trans-membrane flux decreased. This performance reduction in the MD membranes was attributed to the electrostatic attraction between the positively charged surfactant and the negatively charged membrane surface.
Han et al. (Han et al. 2017) studied the effect of the key components (O/W emulsion, surfactant and salts) present in PW on MD process. The results from this study showed that the reduction in MD performance in terms of permeate flux and quality was mainly caused by the presence of salt (namely, sodium chloride) and surfactant (namely, sodium dodecyl sulphate), rather than oil, suggesting the need to remove or dilute the salt or surfactant from oily feeds before MD application.
In general, the addition of salt in a solution containing surfactants may modify the properties of the solution, causing a change in surface tension (Ozdemir et al. 2009) and surfactant critical micelle concentration (CMC) (Corrin et al. 1947). Previous studies have revealed that in the presence of NaCl, the surface tension and CMC of SDS are reduced (Woolfrey et al. 1986; Xu et al. 2009). This reduction can be due to the fact that electrolytes promote the migration of surfactant species to the surface of air/liquids (Eriksson and Ljunggren 1989). Regarding the MD process, a recent molecular dynamics study (Velioğlu et al. 2018) reported the mechanisms underlying severe pore-wetting when both SDS and NaCl are present in the feed solutions. According to this study, NaCl increases the affinity of SDS to the PVDF membrane (without decreasing the mobility of SDS) which leads to a decrease in the surface tension at the pore mouth and thereby to an increase in the likelihood of membrane wetting thus exceeding the liquid entry pressure (LEP).
Also, this study suggests that a pre-treatment of PW may be necessary to separate salts and surfactant prior to applying MD (Han et al. 2017).
In the present study, the impact of oil and surfactant contained in a synthetic PW solution on the MD performance using two different hydrophobic membranes was investigated. For a clear comparative study, a synthetic solution without oil and surfactant was prepared based on the salts that compose actual PW. Moreover, the capacity to simultaneously recover fresh water and high-quality saline products was explored by the MCr process. Oil and surfactant effects on the crystallization kinetics and on the characteristics of the final product were also studied. Additionally, studies on the fouling tendency of the selected membranes were performed.
Materials and methods
Chemicals and membranes
Sodium chloride (NaCl, from VWR Chemicals), calcium chloride bihydrate (CaCl2·2H2O, from VWR Chemicals), magnesium chloride hexahydrate (MgCl2·6H2O, from Sigma-Aldrich), potassium chloride (KCl, from Carlo Erba), sodium sulfate (Na2SO4, from Carlo Erba), and strontium chloride (SrCl2, from Carlo Erba) were used in the preparation of the feed solutions. Commercially available motor oil (SUPER PLUS 10W-40, TotalErg S.p.a, Italy) and sodium dodecyl sulphate, SDS (NaC12H25SO4, from Thermo Fischer Scientific- a common anionic surfactant used in cosmetic and hygienic products), were employed for the preparation of synthetic PW solution. Motor oil and SDS specifications are highlighted in Table 1.
Two types of membranes were utilized in the experimentation: laboratory-made Hyflon AD40H/polyvinylidene fluoride (PVDF) composite membranes and commercial polypropylene (3 M™ Capillary Membrane MF-PP Series, Type S6/2) membranes. The composite membranes were fabricated by dip-coating process. The PVDF fibers utilized as substrate of the composite membranes were fabricated by Thermally Induced Phase Separation (TIPS) in the laboratory of Nanjing Tech University utilizing PVDF (Solef® 6010, powder, kindly supplied by Solvay Specialty Polymers, Shanghai, China) and following the procedure described by Cui et al. (Cui et al. 2018) in which Dibutyl maleate (DBM) was employed as a diluent for PVDF membrane fabrication via TIPS method. The detailed properties of the membranes are summarized in Table 2.
Laboratory-made modules were prepared by potting the fibers with epoxy resin (Stycast 1266, Emerson & Cuming, Belgium) inside glass vessels and then installed on a bench-scale MD system.
Feed solutions: composition and preparation
Two different feed solutions were prepared according to the protocol of (Dardor et al. 2021):
-
(i)
solution without oil and SDS—a background solution based on the ionic composition of actual PWs. The salts used in the recipe are given in Table 3;
-
(ii)
solution with oil and SDS—a synthetic PW solution whose preparation protocol is illustrated in Fig. 1.
Specifically, motor oil was used as the hydrocarbon source and added to the background solution to investigate its effect on the MD and MCr performance. The surfactant was added to the solution to disperse oil droplets in the aqueous phase. In a 500 mL sample, 0.18 mL and 30 mg of oil and SDS were added, respectively.
Distillate water (with composition Mg2+ = 0.17 \(\pm\) 0.01 ppm, \({{\text{Cl}}}^{-}\)= 2.06 \(\pm\) 0.8 ppm; conductibility = 0.015 \(\pm 0.002\) mS/cm) generated in the laboratory using Zeener RO 180 system (Human Corporation, Seoul, Korea) was used to prepare the solutions.
Total organic carbon (TOC) analysis
Total organic carbon (TOC) measurements of the feed solution and of the permeate were carried out using a TOC-V CSN analyzer (Shimadzu Europa GmbH, Germany). This instrument utilizes the standard catalytic oxidation method with a platinum catalyst operating at 680 °C.
MD and MCr set-up description
MD and MCr setup was operated in direct contact configuration mode. Figure 2 shows the scheme of the system used in this work, already described in the literature (Macedonio et al. 2014). Briefly, the feed and distillate were recirculated to the membrane module in counter-current by Masterflex L/S Easy-Load II pump (head model 77,202–50), and Heidolph pump drive 5201, respectively; both feed and distillate flow rates were monitored using flowmeters. The feed was heated by a heater (type M900—TI Basic MPM Instruments srl, Bernareggio, Italy) before entering into the membrane module. Permeate was introduced into the membrane module from the permeate tank. Temperatures were measured by K-element thermocouple thermometers (Hana HI 935002) with sensitivity ± 0.2 °C.
Trans-membrane flux \(\left(J\right)\) was estimated by evaluating weight variations in the permeate tank with a Gibertini EU-C LCD balance (Gibertini Elettronica, Novate Milanese (MI), Italy) (H), and calculated as
where \({m}_{{\text{p}}}\) [L] is the mass of collected permeate, A [m2] is the active membrane area, and Δt [h] is the distillation time. The starting volume of feed and permeate was 500 mL.
The salt rejection (SR) was determined as follows:
where \({c}_{{\text{p}}}\) and \({c}_{{\text{f}}}\) \([{\text{g}}{\mathrm{ L}}^{-1}]\) are the salt concentration of permeate and feed solutions, respectively, estimated by measuring the electrical conductivity of the solutions using a benchtop conductivity meter (Orion Star A212, Thermo Fisher Scientific).
MCr—crystal characterization
An optical microscope (ZEISS, model Axiovert 25) equipped with a camera (VISIOSCOPE Modular System equipped-optical head 10 ÷ 100 ×) was used for the initial and preliminary characterization of the obtained crystals. ImageJ software was used for the processing of the images (Wayne Rasband, http://imagej.nih.gov/ij/).
The chemical composition of the crystal samples was determined by energy-dispersive x-ray spectroscopy (EDX) by using an electron microprobe analyzer (EPMA—Jeol—JXA 8230, 10 kV, 10 nA).
Crystals were characterized in terms of crystal size distribution (CSD), mean diameter (dm), growth (G) and nucleation rate (B0).
CSD was used to evaluate the cumulative percent function and the coefficient of variation (CV):
where \({\text{PD}}\) is the crystal length at the indicated percentage.
Coefficients of variation were evaluated taking into account both the length and the length-to-width ratio of the crystals.
Growth rate (G) and nucleation rate (B0) were estimated on the basis of the Randolph-Larson model:
where n [no. crystals/mm] is the crystal population density, L [μm] is crystal size, G [μm/min] is growth rate, t [min] is retention time and n0 is population density at L equal to zero.
Results and discussion
Oil and SDS influence on direct contact membrane distillation (DCMD) performance
MD tests
The performance of PP and AD40H membranes was evaluated in direct contact membrane distillation (DCMD) module using without oil and SDS and with oil and SDS feed solutions. MD tests were performed over a period of 220 min, at the feed and permeate temperature of \(57.0\pm 0.3\) and \(20.8\pm 0. 4 ^\circ {\text{C}}\), respectively. The investigation was conducted with a feed flow rate of 120 \({\text{L}}/{\text{h}}\) and a permeate flow rate of 5 \({\text{L}}/{\text{h}}\). During each test, the flux was monitored to control the stability and efficiency of the tested membranes.
As shown in Fig. 3, the permeate fluxes remained almost constant throughout the experiments. In detail, using the feed without oil and SDS, trans-membrane fluxes of \(6.9\) and4.8 \({{\text{Lm}}}^{-2}{{\text{h}}}^{-1}\) were observed for the PP and AD40H membranes, respectively. An effective reduction in flux occurred for both membranes when the feed solution was changed to the with oil and SDS solution. Specifically, the presence of oil and SDS in the feed solution resulted in a permeate flux reduction of 20 and 40% for PP and AD40H membranes, respectively. This reduction in the flux can be attributed to the coupling between the salts and SDS which affects their affinity to the membrane, leading to a deterioration in membrane performance (Han et al. 2017; Velioğlu et al. 2018) and thus to the necessity to pre-treat PW before MD application according to literature (Han et al. 2017).
It should be noted that the MD test with the PP membrane without oil and surfactant was carried out at a temperature of the feed equal to about 44 °C, while the one with oil and surfactant was carried out at 43 °C. Instead, in the case of the AD40H membrane, the two tests were carried out at about 43 and 41 °C, respectively. The slightly different temperature difference between the two tests, for the two different membranes, caused the widest difference between the two flux curves observed for AD40H membranes (AD40H without oil and SDS and AD40H with oil and SDS curves in Fig. 3) as compared to that between the two flux curves recorded for PP membranes (PP without oil and SDS and PP with oil and SDS curves in Fig. 3).
Figure 3 also shows that the lowest flux value was obtained with the AD40H membranes for both feed solutions used. The different behavior of the observed fluxes can be mainly justified by the different porosity of the two membranes. As indicated in Table 2, the porosity for AD40H membranes is lower than that for PP, resulting in a lower flux, in accordance to the relationship between the flux J and porosity ɛ shown in Eq. (6)
where ɛ is the overall porosity of the membrane, r is the mean pore size, τ is the tortuosity factor and δ is the membrane thickness. For cylindrical pores, the value of τ is unity. For Knudsen diffusion a = 1, whereas a = 2 for viscous flux (Al-Salmi 2020).
Effect of feed temperature on the permeate flux
The effect of the feed inlet temperature on the transmembrane flux was investigated increasing the feed temperature from 40 to 60 °C and maintaining constant the permeate temperature. The feed and permeate flow rates were kept constant at 120 and 5 L/h, respectively.
Figure 4 reports the trends of the PP and AD40H membranes for the feeds without oil and SDS and with oil and SDS. In both cases, the experimental tests showed that the permeate flux increases with feed temperature.
The fluxes increased from 2.7 to 7.1 \({{\text{Lm}}}^{-2}{{\text{h}}}^{-1}\) for PP membrane and from 0.8 to 4.8 \({{\text{Lm}}}^{-2}{{\text{h}}}^{-1}\) for AD40H membrane with the feed without oil and SDS. Likewise, an increase in flux from 2.2 to 6.4 \({{\text{Lm}}}^{-2}{{\text{h}}}^{-1}\) and from 0.7 to 3.2 \({{\text{Lm}}}^{-2}{{\text{h}}}^{-1}\) was observed for PP and AD40H membranes, respectively, using the feed with oil and SDS.
In MD, the increase in permeate flux with the increase in feed temperature is due to the direct relationship between the flux J and the vapor pressure gradient across the membrane \(\Delta P\)
where C is the membrane distillation coefficient.
Indeed, the vapor pressure increases exponentially with temperature according to the Antoine equation (\(P={e}^{\left(A+\frac{B}{T+C}\right)}\), where A, B and C are specific constants which vary from substance to substance), affecting exponentially the productivity of the process (Alklaibi et al. 2005).
Fouling study
The fouling behaviors of the two membranes were investigated using both feed solutions without oil and SDS and with oil and SDS, at feed and permeate temperatures of \(51.0\pm 3.5 ^\circ {\text{C}}\) and \(20.5\pm 1.5 ^\circ {\text{C}}\), respectively. The tests were carried out with a feed flow rate of \(120\mathrm{ L}/{\text{h}}\) and a permeate flow rate of \(5\mathrm{ L}/{\text{h}}\).
Figure 5 displays a typical fouling study protocol. At first, DCMD tests were conducted using distillate water as feed for 180 min (phase 1). Subsequently, distillate water was replaced by the solutions without oil and SDS or with oil and SDS and the tests ran for 300 min (phase 2). Finally, distillate water was used to clean the membrane surface and the flux was again recorded using distillate water as feed (phase 3). The results of the final phase provided information about the type of fouling, indicating whether any chemical cleaning is required.
The permeate fluxes for the PP and AD40H membranes were stable during phase 2 of all tests performed. In this phase, the salt rejections of the system without oil and SDS were very similar to those of the system with oil and SDS, with values higher than 99.9% (Table 4). The stable permeate flux and high salt rejections proved the lack of membrane wetting. In addition, TOC rejection factors of 80 and 90% were observed for PP and AD40H membranes (Table 4), respectively, suggesting that the DCMD system is sufficiently efficient in rejecting organic compounds treated in this investigation.
For both membranes, the fluxes were recovered to the initial value in phase 3 by simple distillate water cleaning, indicating the absence of severe fouling, which conforms with a previous study by (Al-Salmi et al. 2020). These results hence show that DCMD has great potential for the treatment of PW, with performance that can be restored after a physical membrane cleaning with distilled water (Al-Salmi et al. 2020).
Oil and SDS influence on membrane crystallization performance
MCr pre-treatment—calcium removal
Membrane crystallization is a powerful tool for promoting the formation of crystals of salt from highly concentrated solutions. However, it can suffer from severe scaling depending on the feed composition. Scaling in MCr is usually caused by inorganic salts such as calcium sulfate (CaSO4) and calcium carbonate (CaCO3). In literature (Drioli et al. 2004), it was proven that in order to limit the CaSO4 formation during the concentration of feed solutions, Ca2+ ions can be removed as CaCO3 by reaction with anhydrous sodium carbonate (Na2CO3).
In this work, feed solutions without oil and SDS and with oil and SDS were first chemically treated with Na2CO3 (before MCr tests) and then concentrated up to the point of NaCl crystallization.
The proper Na2CO3 addition was determined with respect to the Ca2+ ion concentration in the feed and the amount of Ca2+ ions removed. In particular, four feed solution samples were mixed with Na2CO3 in different molar ratios (1:1, 1:2, 1:3, 1:4) in order to promote CaCO3 formation and precipitation. The solutions with the precipitated CaCO3 were then filtered to remove the particles precipitated, and the filtrated solutions were analyzed via advanced Compact ion chromatographer 861 (Metrohm AG, Switzerland) to quantify the concentration of Ca2+ ions in each diluted mixture. The obtained results (Fig. 6) prove that the Ca2+ ions contribution became practically negligible when Na2CO3 was added in a 1:3 molar ratio of Ca2+/\({{\text{CO}}}_{3}^{-}\).
MCr tests and fouling study
As a result of their better DCMD performance (in terms of flux), PP membranes were selected for further MCr tests.
Figure 7 shows the time-dependent permeate flux profiles obtained for the feed solutions without oil and SDS and with oil and SDS at feed inlet temperature of \(51.7\pm 0.5^\circ {\text{C}}\). The fluxes (observed in phase 2) did not decrease significantly when NaCl supersaturation was achieved (after 520 and 1190 min for the feed solutions without oil and SDS and with oil and SDS, respectively). Therefore, all MCr tests were carried out with almost constant flux, demonstrating a good operational status.
For feed solution without oil and SDS, the average flux was around \(3.4 {{\text{Lm}}}^{-2}{{\text{h}}}^{-1}\) which is higher than that obtained by treating the solution with oil and SDS (\(\sim 2.2\mathrm{ L}{{\text{m}}}^{-2}{{\text{h}}}^{-1}\)) under the same operating conditions (feed flow rate = 120 L/h, permeate flow rate = 5 L/h). The results demonstrate again that the presence of oil and SDS in the feed causes a decrease in trans-membrane flux which, as mentioned above, can be attributed to the interaction between the salts and SDS surfactant affecting negatively the efficiency of the PP membrane according to Han et al. (Han et al. 2017).
Furthermore, experiments with water as feed have been carried out before and after the tests conducted using the feed solutions without oil and SDS and with oil and SDS (Fig. 7), in order to analyze the effect of fouling on the performance of the MCr. Initial fluxes were recovered after cleaning with only water, proving that severe membrane fouling did not occur during MCr experiments. These results have shown the high capacity of the MCr process to treat hypersaline PW solution, in line with the DCMD results reported in Sect. "Fouling study".
The properties of the obtained permeate (Table 5) showed very interesting results in terms of salt rejection rate. PP membranes exhibited high salt rejection values (99.8–99.9%) for both used feed solutions, indicating that salt infiltration through the membrane pores for feed without oil and SDS and for feed with oil and SDS was negligible; therefore PP membrane preserved its intrinsic hydrophobic nature during the investigation.
In presence of oil and SDS, MCr process achieved a water recovery factor of 32% after \(\Delta {t}_{2}= 1280 {\text{min}}\) of operation. However, a water recovery factor of 22% was obtained by treating the feed without oil and SDS in a much shorter operation time (\(\Delta {t}_{1}= 600 {\text{min}})\). At the end of the tests without oil and SDS and with oil and SDS, the total water recovery factors achieved were of 99 and 97%, respectively.
NaCl crystallization kinetics
Continuous removal of the water vapors from the feed solution induces its saturation and the formation of NaCl crystals. After the induction time, for each MCr test three different solution samples were extracted from the feed tank (the first one at crystallization onset, the second after 30 min, and the third after 1 h) and analyzed using an optic microscope in order to determine crystals shape, dimension, and crystal size distribution. As mentioned above, obtained crystals were characterized in terms of dm, CV, G, and B0 whose values are reported in Table 6.
For without oil and SDS system, dm and G values increased from sample 1 to sample 2, whereas decreased from sample 2 to sample 3. This tendency was due to the fact that the nucleation mainly occurred in sample 1 (as proved by the very high B0 value of sample 1). Increased values of G and reduced values of B0 in samples 2 and 3 (compared to G and B0 values obtained for sample 1) increased the crystal size distribution, giving higher CV values.
A similar trend was observed for the with oil and SDS system, where dm and G values increased due to the decrease in B0. Moreover, the presence of oil and SDS increased the induction time compared to the feed without oil and SDS, from 520 to 1190 min for the feed containing oil and SDS.
Figure 8 shows the trend of CSDs for the NaCl crystals produced in both the carried out MCr tests without oil and SDS and with oil and SDS. In both cases, the initial peak of the distributions moves toward larger dimensions from sample 1 to sample 2, as a result of crystals growth, whereas slightly smaller dimensions were revealed from samples 2 to samples 3 (as proved also by dm, B0, and G values reported in Table 6). A more uniform distribution of NaCl crystals was obtained using the feed without oil and SDS, proved by the lower CV values in comparison with those achieved by employing the solution with oil and SDS as feed. Nonetheless, good values of CV were also obtained for the system with oil and SDS, confirming a narrow size distribution of the crystals and, thus, a good quality of the product (Curcio 2005).
The optical microscope images reported in Fig. 9 and related to the NaCl crystals obtained in sample 1 for the two feeds without oil and SDS and with oil and SDS are in agreement with the results reported in Table 6: numerous and more uniform crystals (B0 = 133,358 and CV = 38.5%) were observed in absence of oil and SDS, whereas less numerous and different crystals were obtained with the solution containing oil and SDS (B0 = 81,041 and CV = 51.74%).
Regarding crystal size, larger NaCl crystals were produced at the end of the experiments by treating the solution with oil and SDS (see dm values of sample 3 in Table 6), as also confirmed by the CDS analysis.
From microscopic pictures, crystals showed mainly the typical cubic block-like form in accordance with the expected geometry of the NaCl crystals. Nevertheless, it was observed that in all samples analyzed, a small amount of crystals exhibited an elongated shape. Consequently, the length/width ratio was estimated for each crystal observed. Figure 10 shows the length/width ratio for the three samples obtained from feed solutions without oil and SDS and with oil and SDS. The obtained results indicated that, in each analyzed sample, most of the crystals had a length/width ratio in the range of 1.0–1.3, confirming the cubic structure of the produced NaCl crystals. In addition, a higher number of cubic block-like crystals were observed in the solution without oil and SDS. This is probably due to the fact that the presence of small quantities of foreign substances in the solution may alter the crystal habit. Therefore, the oil and surfactant present in the crystallizing solution might have influenced negatively the crystal shape of NaCl crystals. Their presence should be controlled to obtain more regular shape crystals.
The composition of observed crystals has been investigated by EDX analysis. In Fig. 11, EDX spectra show that both crystals obtained without and with oil and SDS in the feed were mainly composed of sodium and chloride, with a very small amount of calcium still present in the feed solution despite calcium carbonate precipitation. Therefore, the chemical composition of the crystals is not affected by the presence of oil or surfactant in the feed. EDX measurements thereby proved the good purity of the final products.
Conclusions
The aim of this work was to study the effect of the oil and surfactant present in a synthetic PW feed on the performance of MD and MCr processes. For comparison, a synthetic background solution based on actual PW salts, without oil and surfactant, was also prepared. Polypropylene and Hyflon AD40H/PVDF composite membranes were tested in DCMD process, while MCr experiments were conducted with only PP membranes.
The main conclusions of this study are summarized as follow:
In DCMD experiments, flux reduction was observed for PP and AD40H membranes which can be attributed to the combined presence of salts and surfactant in the feed solution. This suggested that a pre-treatment for PW solutions prior to MD application is necessary to remove salts or surfactants, according to the literature.
For both solutions without and with oil and SDS, the lowest flux values were obtained for AD40H membrane due to its lowest porosity with respect PP membrane. As expected, the permeate flux of the two membranes increased with increasing the operating temperature of MD.
In presence of oil and SDS, high salt rejections (> 99.9%) and good TOC performance (80 and 90% for PP and AD40H membranes, respectively) were achieved in both lab-made membrane modules (PP and AD40H), confirming the good quality of the permeate.
Long-term tests showed DCMD performance stability and minimal reversible fouling. Moreover, a simple washing with distillate water recovered the initial permeate flux of the membranes in the performed tests. Stable fluxes were observed during all MCr experiments performed with PP membranes. However, the performance of MCr was reduced by 35% in the presence of oil and surfactant. Similar to what was observed in MD tests, this behavior could be due to the coupling between salts and SDS which deteriorates the MCr performance in terms of permeate flux. In this work, only a physical method (distillate water washing) was studied, as no serious fouling was observed. A total water recovery factor of 97% was achieved for the solution with oil and SDS.
In addition, in presence of oil and surfactant, good quality NaCl crystals were produced by MCr process, with uniform size distribution and a good cubic structure. However, oil and SDS presence in the feed involved an increase in the induction time with respect to the system without oil and SDS.
References
Abbasi M, Salahi A, Mirfendereski M, Mohammadi T, Pak A (2010) Dimensional analysis of permeation flux for microfiltration of oily wastewaters using mullite ceramic membranes. Desalination 252(1–3):113–119. https://doi.org/10.1016/j.desal.2009.10.015
Ahmad NA, Goh PS, Yogarathinam LT, Zulhairun AK, Ismail AF (2020) Current advances in membrane technologies for produced water desalination. Desalination 493:114643. https://doi.org/10.1016/j.desal.2020.114643
Ali A, Quist-Jensen CA, Drioli E, Macedonio F (2018) Evaluation of integrated microfiltration and membrane distillation/crystallization processes for produced water treatment. Desalination 434:161–168. https://doi.org/10.1016/j.desal.2017.11.035
Alkhudhiri A, Darwish N, Hilal N (2012) Membrane distillation: a comprehensive review. Desalination 287:2–18. https://doi.org/10.1016/j.desal.2011.08.027
Alklaibi AM, Lior N (2005) Membrane-distillation desalination: Status and potential. Desalination 171:111–131. https://doi.org/10.1016/j.desal.2004.03.024
Al-Salmi M, Laqbaqbi M, Al-Obaidani S, Al-Maamari RS, Khayet M, Al-Abri M (2020) Application of membrane distillation for the treatment of oil field produced water. Desalination 494:114678. https://doi.org/10.1016/j.desal.2020.114678
Ameen NAM, Ibrahim SS, Alsalhy QF, Figoli A (2020) Highly saline water desalination using direct contact membrane distillation (DCMD): experimental and simulation study. Water 12(6):1575. https://doi.org/10.3390/w12061575
Boukhriss M, Timoumi M, Bacha HB (2023a) Experimental of membrane distillation unit coupled with a DCMD using solar energy. Solar Compass 7:100055. https://doi.org/10.1016/j.solcom.2023.100055
Boukhriss M, Maatoug MA, Farhani S, Timoumi M, Jammali A, Bacha HB (2023b) Experimental validation of membrane distillation unit coupled with a sweeping gas membrane using solar energy. Int J Low Carbon Technol 18:999–1007. https://doi.org/10.1093/ijlct/ctad109
Chakrabarty B, Ghoshal AK, Purkait MK (2008) Ultrafiltration of stable oil-in-water emulsion by polysulfone membrane. J Membr Sci 325(1):427–437. https://doi.org/10.1016/j.memsci.2008.08.007
Chang H, Li T, Liu B, Chen C, He Q, Crittenden JC (2019) Smart ultrafiltration membrane fouling control as desalination pretreatment of shale gas fracturing wastewater: The effects of backwash water. Environ Int 130:104869. https://doi.org/10.1016/j.envint.2019.05.063
Chen Y, Tian M, Li X, Wang Y, An AK, Fang J, He T (2017) Anti-wetting behavior of negatively charged superhydrophobic PVDF membranes in direct contact membrane distillation of emulsified wastewaters. J Membr Sci 535:230–238. https://doi.org/10.1016/j.memsci.2017.04.040
Coha M, Farinelli G, Tiraferri A, Minella M, Vione D (2021) Advanced oxidation processes in the removal of organic substances from produced water: potential, configurations, and research needs. Chem Eng J 414:128668. https://doi.org/10.1016/j.cej.2021.128668
Corrin ML, Harkins WD (1947) The effect of salts on the critical concentration for the formation of micelles in colloidal electrolytes 1. J Am Chem Soc 69(3):683–688. https://doi.org/10.1021/ja01195a065
Cui Z, Cheng Y, Xu K, Yue J, Zhou Y, Li X, Wang Q, Sun SP, Wang Y, Wang X, Wang Z (2018) Wide liquid-liquid phase separation region enhancing tensile strength of poly (vinylidene fluoride) membranes via TIPS method with a new diluent. Polymer 141:46–53. https://doi.org/10.1016/j.polymer.2018.02.054
Curcio E, Drioli E (2005) Membrane distillation and related operations — a review. Sep Purif Rev 34(1):35–86. https://doi.org/10.1081/SPM-200054951
Dardor D, Al-Maas M, Minier-Matar J, Janson A, Sharma R, Hassan MK, Al-Maadeed MAA, Adham S (2021) Protocol for preparing synthetic solutions mimicking produced water from oil and gas operations. ACS Omega 6(10):6881–6892. https://doi.org/10.1021/acsomega.0c06065
Dastgheib SA, Knutson C, Yang Y, Salih HH (2016) Treatment of produced water from an oilfield and selected coal mines in the Illinois Basin. Int J Greenh Gas Control 54:513–523. https://doi.org/10.1016/j.ijggc.2016.05.002
Dilaver M, Hocaoğlu SM, Soydemir G, Dursun M, Keskinler B, Koyuncu I, Ağtaș M (2018) Hot wastewater recovery by using ceramic membrane ultrafiltration and its reusability in textile industry. J Clean Prod 171:220–233. https://doi.org/10.1016/j.jclepro.2017.10.015
Dinar A, Tieu A, Huynh H (2019) Water scarcity impacts on global food production. Glob Food Sec 23:212–226. https://doi.org/10.1016/j.gfs.2019.07.007
Drioli E, Curcio E, Criscuoli A, Di Profio G (2004) Integrated system for recovery of CaCO3, NaCl and MgSO4· 7H2O from nanofiltration retentate. J Membr Sci 239(1):27–38. https://doi.org/10.1016/j.memsci.2003.09.028
Eriksson JC, Ljunggren S (1989) A molecular theory of the surface tension of surfactant solutions. Colloids Surf 38(1):179–203. https://doi.org/10.1016/0166-6622(89)80153-2
Estrada JM, Bhamidimarri R (2016) A review of the issues and treatment options for wastewater from shale gas extraction by hydraulic fracturing. Fuel 182:292–303. https://doi.org/10.1016/j.fuel.2016.05.051
Fakhru’l-Razi A, Pendashteh A, Abdullah LC, Biak DRA, Madaeni SS, Abidin ZZ, (2009) Review of technologies for oil and gas produced water treatment. J Hazard Mater 170(2–3):530–551. https://doi.org/10.1016/j.jhazmat.2009.05.044
Franken ACM, Nolten JAM, Mulder MHV, Bargeman D, Smolders CA (1987) Wetting criteria for the applicability of membrane distillation. J Membr Sci 33(3):315–328. https://doi.org/10.1016/S0376-7388(00)80288-4
Goh PS, Wong KC, Ismail AF (2022) Membrane technology: a versatile tool for saline wastewater treatment and resource recovery. Desalination 521:115377. https://doi.org/10.1016/j.desal.2021.115377
González D, Amigo J, Suárez F (2017) Membrane distillation: perspectives for sustainable and improved desalination. Renew Sust Energ Rev 80:238–259. https://doi.org/10.1016/j.rser.2017.05.078
Gryta M (2020) Separation of saline oily wastewater by membrane distillation. Chem Pap 74(7):2277–2286. https://doi.org/10.1007/s11696-020-01071-y
Gryta M, Karakulski K (1999) The application of membrane distillation for the concentration of oil-water emulsions. Desalination 121(1):23–29. https://doi.org/10.1016/S0011-9164(99)00004-1
Gryta M, Karakulski K, Morawski AW (2001) Purification of oily wastewater by hybrid UF/MD. Water Res 35(15):3665–3669. https://doi.org/10.1016/S0043-1354(01)00083-5
Han L, Tan YZ, Netke T, Fane AG, Chew JW (2017) Understanding oily wastewater treatment via membrane distillation. J Membr Sci 539:284–294. https://doi.org/10.1007/s11696-020-01071-y
Hong A, Fane AG, Burford R (2003) Factors affecting membrane coalescence of stable oil-in-water emulsions. J Membr Sci 222(1–2):19–39. https://doi.org/10.1016/S0376-7388(03)00137-6
Huang Z, Liu X, Sun S, Tang Y, Yuan X, Tang Q (2021) Global assessment of future sectoral water scarcity under adaptive inner-basin water allocation measures. Sci Total Environ 783:146973. https://doi.org/10.1016/j.scitotenv.2021.146973
Igunnu ET, Chen GZ (2014) Produced water treatment technologies. Int J Low-Carbon Technol 9(3):157–177. https://doi.org/10.1093/ijlct/cts049
Igwe CO, Saadi AA, Ngene SE (2013) Optimal options for treatment of produced water in offshore petroleum platforms. J Pollut Eff Cont 1(2):1–5. https://doi.org/10.4172/2375-4397.1000102
Jiménez SM, Micó MM, Arnaldos M, Medina F, Contreras S (2018) State of the art of produced water treatment. Chemosphere 192:186–208. https://doi.org/10.1016/j.chemosphere.2017.10.139
Kargbo DM, Wilhelm RG, Campbell DJ (2010) Natural gas plays in the Marcellus shale: Challenges and potential opportunities. Environ. Sci. Technol 44(15):5679–5684. https://doi.org/10.1021/es903811p
Karimnezhad H, Rajabi L, Salehi E, Derakhshan AA, Azimi S (2014) Novel nanocomposite Kevlar fabric membranes: Fabrication characterization, and performance in oil/water separation. Appl Surf Sci 293:275–286. https://doi.org/10.1016/j.apsusc.2013.12.149
Kim ES, Liu Y, El-Din MG (2011) The effects of pretreatment on nanofiltration and reverse osmosis membrane filtration for desalination of oil sands process-affected water. Sep Purif Technol 81(3):418–428. https://doi.org/10.1016/j.seppur.2011.08.016
Macedonio F, Ali A, Poerio T, El-Sayed E, Drioli E, Abdel-Jawad M (2014) Direct contact membrane distillation for treatment of oilfield produced water. Sep Purif Technol 126:69–81. https://doi.org/10.1016/j.seppur.2014.02.004
Motta A, Borges C, Esquerre K, Kiperstok A (2014) Oil produced water treatment for oil removal by an integration of coalescer bed and microfiltration membrane processes. J Membr Sci 469:371–378. https://doi.org/10.1016/j.memsci.2014.06.051
Nasiri M, Jafari I, Parniankhoy B (2017) Oil and gas produced water management: a review of treatment technologies, challenges, and opportunities. Chem Eng Commun 204(8):990–1005. https://doi.org/10.1080/00986445.2017.1330747
Ozdemir O, Karakashev SI, Nguyen AV, Miller JD (2009) Adsorption and surface tension analysis of concentrated alkali halide brine solutions. Miner Eng 22(3):263–271. https://doi.org/10.1016/j.mineng.2008.08.001
Ricceri F, Giagnorio M, Farinelli G, Blandini G, Minella M, Vione D, Tiraferri A (2019) Desalination of produced water by membrane distillation: Effect of the feed components and of a pre-treatment by fenton oxidation. Sci Rep 9(1):14964. https://doi.org/10.1038/s41598-019-51167-z
Sadrzadeh M, Pernitsky D, McGregor M (2018) Nanofiltration for the treatment of oil sands-produced water. Rijeka InTech. https://doi.org/10.5772/intechopen.74086
Silalahi SH, Leiknes T (2009) Cleaning strategies in ceramic microfiltration membranes fouled by oil and particulate matter in produced water. Desalination 236(1–3):160–169. https://doi.org/10.1016/j.desal.2007.10.063
Tomer N, Mondal S, Wandera D, Wickramasinghe SR, Husson SM (2009) Modification of nanofiltration membranes by surface-initiated atom transfer radical polymerization for produced water filtration. Sep Sci Technol 44(14):3346–3368. https://doi.org/10.1080/01496390903212540
Veil JA (2011) Produced water management options and technologies. Produced Water: Environ Risks Adv Mitig Technol. https://doi.org/10.1007/978-1-4614-0046-2_29
Velioğlu S, Han L, Chew JW (2018) Understanding membrane pore-wetting in the membrane distillation of oil emulsions via molecular dynamics simulations. J Membr Sci 551:76–84. https://doi.org/10.1016/j.memsci.2018.01.027
Wandera D, Wickramasinghe SR, Husson SM (2011) Modification and characterization of ultrafiltration membranes for treatment of produced water. J Membr Sci 373(1–2):178–188. https://doi.org/10.1016/j.memsci.2011.03.010
Wang P, Chung TS (2015) Recent advances in membrane distillation processes: Membrane development, configuration design and application exploring. J Membr Sci 474:39–56. https://doi.org/10.1016/j.memsci.2014.09.016
Wang X, Goual L, Colberg PJ (2012) Characterization and treatment of dissolved organic matter from oilfield produced waters. J Hazard Mater 217:164–170. https://doi.org/10.1016/j.jhazmat.2012.03.006
Wang Z, Hou D, Lin S (2016) Composite membrane with underwater-oleophobic surface for anti-oil-fouling membrane distillation. Environ Sci Technol 50(7):3866–3874. https://doi.org/10.1021/acs.est.5b05976
Wang Z, Chen Y, Sun X, Duddu R, Lin S (2018) Mechanism of pore wetting in membrane distillation with alcohol vs. surfactant. J Membr Sci 559:183–195. https://doi.org/10.1016/j.memsci.2018.04.045
Woolfrey SG, Banzon GM, Groves MJ (1986) The effect of sodium chloride on the dynamic surface tension of sodium dodecyl sulfate solutions. J Colloid Interface Sci 112(2):583–587. https://doi.org/10.1016/0021-9797(86)90129-3
Xu L, Davis TA, Porter NA (2009) Rate constants for peroxidation of polyunsaturated fatty acids and sterols in solution and in liposomes. J Am Chem Soc 131(36):13037–13044. https://doi.org/10.1021/ja9029076
Zheng J, Chen B, Thanyamanta W, Hawboldt K, Zhang B, Liu B (2016) Offshore produced water management: A review of current practice and challenges in harsh/Arctic environments. Mar Pollut Bull 104(1–2):7–19. https://doi.org/10.1016/j.marpolbul.2016.01.004
Funding
The Nederlandse organisatie voor wetenschappelijk onderzoek (NWO) is gratefully acknowledged for partially funding this work through the project RECOVERY OF VALUABLE MINERALS WITH HYBRID CERAMIC MEMBRANE CRYSTALLIZATION (acronym: ReValue, project number 19954 of the Open Technology research program partly financed by the Dutch Research Council (NWO)).
Author information
Authors and Affiliations
Corresponding author
Ethics declarations
Conflict of interest
The authors declare there is no conflict of interest.
Ethical approval
Not applicable.
Additional information
Publisher's Note
Springer Nature remains neutral with regard to jurisdictional claims in published maps and institutional affiliations.
Rights and permissions
Open Access This article is licensed under a Creative Commons Attribution 4.0 International License, which permits use, sharing, adaptation, distribution and reproduction in any medium or format, as long as you give appropriate credit to the original author(s) and the source, provide a link to the Creative Commons licence, and indicate if changes were made. The images or other third party material in this article are included in the article's Creative Commons licence, unless indicated otherwise in a credit line to the material. If material is not included in the article's Creative Commons licence and your intended use is not permitted by statutory regulation or exceeds the permitted use, you will need to obtain permission directly from the copyright holder. To view a copy of this licence, visit http://creativecommons.org/licenses/by/4.0/.
About this article
Cite this article
Alessandro, F., Macedonio, F., Frappa, M. et al. Freshwater and minerals recovery from synthetic produced water by membrane distillation/membrane crystallization processes. Appl Water Sci 14, 104 (2024). https://doi.org/10.1007/s13201-024-02170-x
Received:
Accepted:
Published:
DOI: https://doi.org/10.1007/s13201-024-02170-x